Pulp molding, as a popular green packaging representative, is favored by brand owners. In the production process of pulp molded products, the mold, as a key component, has high technical requirements for development and design, high investment, long cycle, and high risk. So, what are the key points and precautions in the design of paper plastic molds? Below, we will share some experience in packaging structure design for you to learn and explore pulp molding mold design.
01 Forming Mold
The structure consists of a convex mold, a concave mold, a mesh mold, a mold seat, a mold back cavity, and an air chamber. The mesh mold is the main body of the mold. As the mesh mold is woven from metal or plastic wires with a diameter of 0.15-0.25mm, it cannot be independently formed and must be attached to the surface of the mold to work.
The back cavity of a mold is a cavity composed of a certain thickness and shape that is completely synchronized with the working surface of the mold, relative to the mold seat. The convex and concave molds are a shell with a certain wall thickness. The working surface of the mold is connected to the back cavity by uniformly distributed small holes.
The mold is installed on the template of the molding machine through the mold seat, and an air chamber is installed on the other side of the template. The air chamber is connected to the back cavity, and there are also two channels for compressed air and vacuum on it.
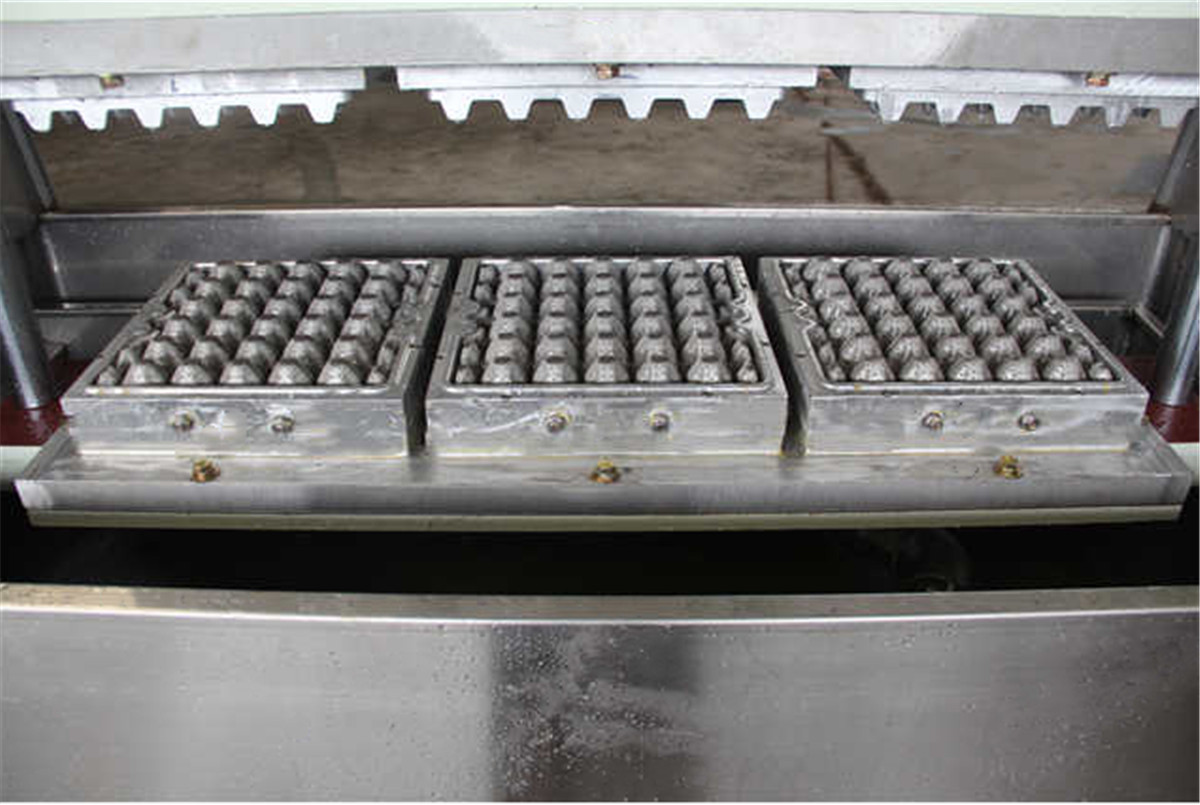
02 Shaping mold
The shaping mold is a mold that directly enters the wet paper blank after forming and has functions of heating, pressurization, and dehydration. The products manufactured with the shaping mold have a smooth surface, accurate dimensions, solidity, and good rigidity. Disposable tableware is made using this mold. In industrial packaging, some small, precise, and large quantities of small items are packaged layer by layer, with packaging products used for positioning between each layer. If pulp molded products are used, they need to be manufactured using molding molds.
However, most industrial packaging products work on one side and do not require heat setting. They can be directly dried. The structure of the shaping mold includes a convex mold, a concave mold, a mesh mold, and a heating element. The convex or concave mold with a mesh mold has drainage and exhaust holes. During operation, the wet paper blank is first squeezed inside the shaping mold, and 20% of the water is squeezed and discharged. At this time, the water content of the wet paper blank is 50-55%, which causes the remaining water after the wet paper blank is heated inside the mold to be vaporized and discharged. The wet paper blank is pressed, dried, and shaped to form a product.
The mesh mold in the molding mold can cause mesh marks on the surface of the product, and the mesh mold can quickly damage during frequent extrusion. To solve this problem, a mold designer has designed a mesh free mold, which is manufactured using copper based spherical powder metallurgy. Over the past two years, after multiple structural improvements and the selection of appropriate powder particle size, the lifespan of the mesh free shaping mold produced is 10 times that of the mesh mold, with a 50% cost reduction. The paper products produced have high precision and smooth inner and outer surfaces.
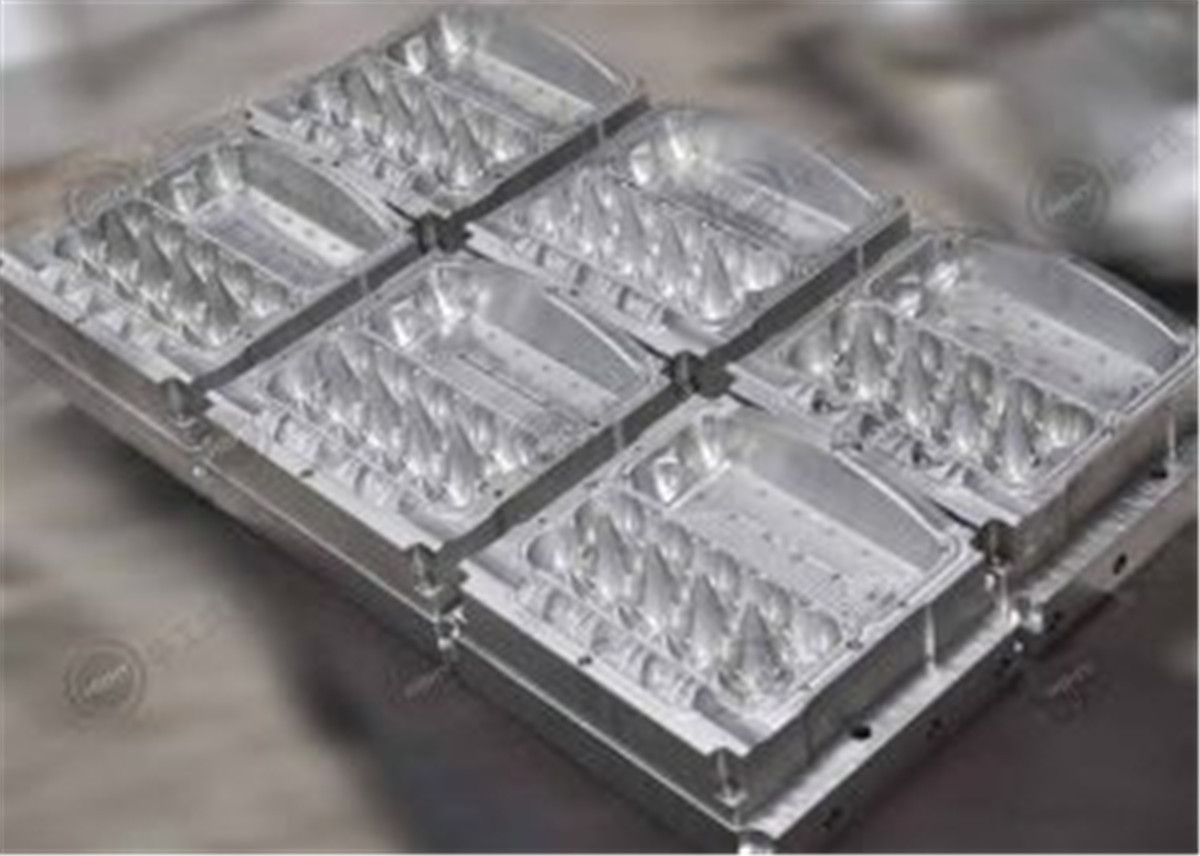
03 Hot Pressing Mold
After drying, the wet paper blank undergoes deformation. When some parts undergo severe deformation or require high precision in the appearance of the product, the product undergoes a shaping process, and the mold used is called a shaping mold. This mold also requires heating elements, but it can be done without a mesh mold. Products that require shaping should retain a moisture content of 25-30% during drying to facilitate shaping.
In production practice, it is difficult to control the water content, which makes it difficult for the product to meet the quality requirements. A manufacturer has designed a spray shaping mold, and spray holes are made on the mold corresponding to the parts that need shaping. When working, the products are put into the shaping mold after being thoroughly dried. At the same time, the spray hole on the mold is used for spray hot pressing the products. This mold is somewhat similar to the spray iron in the clothing industry.
04 Transfering Mold
The transfer mold is the last workstation of the entire process, and its main function is to safely transfer the product from the integral auxiliary mold to the receiving tray. For the transfer mold, its structural design needs to be as simple as possible, with evenly arranged suction holes to ensure that the product can smoothly adsorb on the mold surface.
05 Trimming Mold
In order to make paper molded products clean and beautiful, paper molded products with high appearance requirements are equipped with edge cutting processes. Die cutting molds are used to trim the rough edges of paper molded products, also known as edge cutting molds.
Post time: Oct-20-2023